Since Congress passed the Occupational Safety and Health Act of 1970 and created OSHA (Occupational Safety and Health Administration), working conditions have become safer and more healthy for American workers. The caveat is when companies ignore the standards, intentionally or unintentionally. When that happens, OSHA fines them. Knowing how to prevent them can help ensure that businesses can remain in operation and keep workers safe.
Preventing OSHA violations is important for the future of the business and the health and safety of its employees.
People don’t want to work for companies that put their health and safety in jeopardy, yet it happens. There are several ways businesses can reduce their chances of receiving OSHA fines. These three are the most common:
- Let employees speak without fear of retribution.
A company’s workforce is out in the field or on the ground every day. They can see potential problems and hazards more easily than management, who aren’t “out there” on a daily basis. When employees can report hazards anonymously or without fear, management can then handle the situation. Additionally, designated employees who have received training about OSHA standards can perform regular safety checks to make sure that the workplace is compliant.
- Use technology to your advantage.
Everyone has smart phones and tablets these days, so remain compliant by leaning on mobile technology. When you let technology and mobile apps track data and evaluate processes and procedures in real time, it’s easy to know if you’re following the rules. It also can save you time and money without using outdated processes and relying on paperwork.
- Develop a prevention plan.
Educate workers on OSHA standards. Conduct surprise workplace inspections similar to those OSHA conducts. The stakes are really high, so putting a plan in force early can be very helpful.
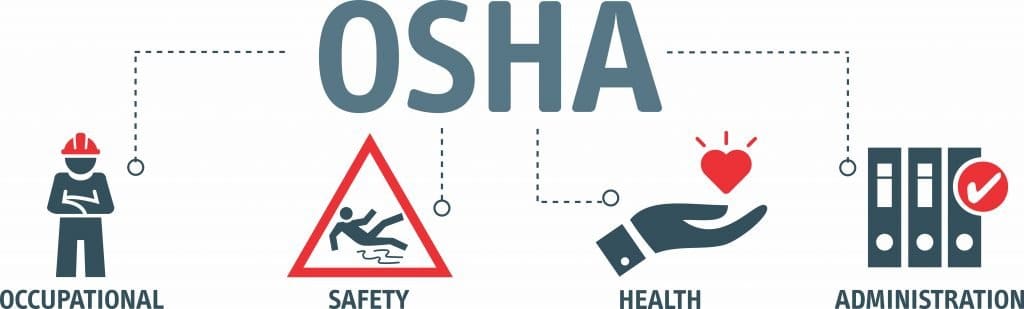
If your company receives an OSHA fine, it’s no slap on the wrist. It can be very costly. As of January 2020, the average OSHA fine for a first-time serious offense is $13,494. If the organization fails to abate by the specified time, the fine increases to the same amount PER DAY beyond the abatement date. For repeated or willful offenses, the fine increases tenfold to $134,937 per offense. That can break many companies.
OSHA determines penalties by the gravity of the violation, and that requires assessing the severity of the illness or injury that could result from the offense—and the probability that one could occur. Other factors, such as the company’s size, history of previous violations and the employer’s “good faith” carry some weight. For example, OSHA realizes that some smaller companies may not have the expertise or resources to recognize some safety hazards.
OSHA provides a list of standards and regulations to all companies, which they must post in a public location—often in their company’s lounge or lunchroom. That enables employees to know the rules and can tell if their company is violating any of them and risking their health or safety.
OSHA issues thousands of citations and fines to businesses every year for violating their standards. Some may seem really insignificant, such as not having a fully stocked first aid kit on premises, having electrical outlets that are missing protective covers, lacking OSHA employee training records when requested and not inspecting office ladders. These are the 10 most cited OSHA violations:
• Protection against falls (general requirements)
• Protection against falls (training requirements)
• Communication about hazards
• Safe scaffolding issues
• Respiratory protection
• Ladder safety
• Lockout/tagout of machine startup
• Powered industrial trucks
• Machine guarding
• Face and eye protection
Although OSHA has the authority to fine companies for violating their rules, maximum fines for even repeat offenders are rate. Quite often, OSHA negotiates lower fines in exchange for fixing the problem that created the violation. The guidelines imposed by Congress set the minimum safety standards that can be enforced by inspections. The main problem is that there are not enough OSHA personnel to inspect all workplaces. The best they can do is watch out for unscrupulous employers or repeat offenders.
In 2015, OSHA upped its practice from going back three years to five years to establish repeat violations, but that’s not really bound by law, according to the United States Court of Appeals for the 2nd Circuit. However, OSHA’s Field Operations Manual (FOM)—their guiding document for enforcing regulations—generally considers a repeat violation to have occurred within five years of the previous citation or final abatement date.
If a an OSHA violation results in a Citation and Notification of Penalty, companies must follow established procedures.
• Post the citation or a copy of it near the place where the violation occurred. This makes employees aware of the hazards. It must remain there for three working days or until the violation is remedied, whichever is longer.
• Post abatement certification documents near the site of the violation.
• If you agree with the violation, correct the condition by the set (abatement) date and pay the penalty, if given one.
• If you disagree, you have 15 working days from the date you receive the citation to contest it in writing.
• You may also request an informal conference with the area OSHA director to discuss the violation.
Train forklift drivers.
According to OSHA, forklifts account for nearly 100,000 injuries per year. There are about 900,000 forklifts operating in workplaces, so that’s almost a 1 in 10 chance that each will be involved in some type of accident every year. Maintaining safe conditions and training the forklift drivers could reduce injuries and accidents, as well as your company’s chance of receiving an OSHA citation and/or penalty.
Heavy equipment training and safety
Since so many workplace injuries involve forklifts and heavy equipment, it’s critical that their drivers have been properly trained on their operation and safety. Heavy Equipment Colleges of America offers training programs designed to help you become an effective and safe worker. Choose to train for a Certificate of Heavy Equipment Operations Level I, Level II, Mobile Crane and Lattice Boom Crawler; each level is three weeks of study. You can also train for an Associate of Applied Science in Construction Management degree (available only at HEC’s Georgia location).
For more information, contact HEC today.